
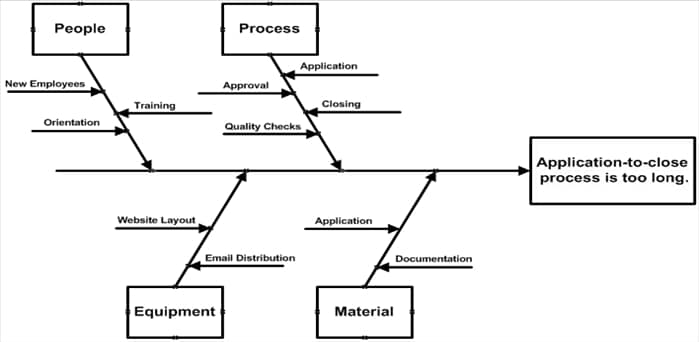
The moderator will continue to ask “why” the problem has occurred. Some of the generic categories could include “Methods”, “People”, “Machines”, “Environment”, “Materials” and may be other relevant categories.For each of the factors, identify the underlying root causes. The problem can be written at the end of the central line at the mouth of the fish.Identify the major factors that may be relevant for this problem. Let the problem be defined in detail, all who contribute to the problem must be identified details of where the problem occurs must be listed. Below are the steps which are to be followed for using this technique effectively.Typically a chart paper or a white board is used for capturing the findings from brain storming session.Describe the problem statement clearly ensuring the all parties involved agree on the same. This needs to be done in a structured manner and it is important to understand all the causes contributing to the defect or the problem. The above diagram presents a sample example of a cause and effect diagram. The team engages in analysing the each of the problems/defects trying to find the root causes of these problems.

Root cause analysis very often is done as a brainstorming activity involving the team members. The mouth or head of the fish depicts the problem, and various bones depict the possible root causes. This technique is a very simple yet one of the most effective techniques and tool for determining root causes of various problems/defects we face in production or in the projects.Cause and effect diagram has become now a very commonly used technique for analysing any kind of organizational problems, not necessarily only quality related problems. The fishbone diagram is a visual way of analysing and capturing the cause and effect. This in turn ensures maintaining both the top lines and bottom lines of businesses.Cause and Effect Diagram, alternatively also known as Fishbone Diagram, was conceived by Japanese Quality Management Guru Ishikawa-san.
#FISHBONE DIAGRAM CAUSE AND EFFECT FREE#
It is of paramount importance for organizations to deliver a defect free product to customers, built in the most efficient manner, thereby ensuring customer satisfaction. For example, in order to verify some of the possible causes identified you may need to collect data (using checksheets) and analyse it (Pareto Analysis, graphs, etc.).Project Management Tutorial By KnowledgeHut Quality Management has gained utmost significance in today’s business. This will probably involve using other tools. If the diagram becomes too crowded, move one or more categories to a new sheet of paper.Įvaluate and analyse the possible causes. Connect them to the main line with slanting arrows.Īdd the causes to the diagram clustered around the major causes they influence.ĭivide and sub-divide the causes to show how they interact, and draw links between causes that are related. Write the major categories in boxes parallel to, and some distance from, the main line. When the effect results from a recognisable process or set of activities, the major steps in the process can be used. Using standard categories such as the 4Ms (Machines, Materials, Methods, Manpower) or PEMPEM (Plant, Equipment, Materials, People, Environment, Methods).Write the effect (problem) in a box on the right and draw a long line pointing to the box.ĭecide the major categories of causes. It must be stated in clear and concise terms, agreed by everyone. The effect may be either a problem or a desirable effect - when something desirable has happened it is useful to find out what caused it so you can make it happen again.Įstablish what the problem, or effect, is. Use this tool when you want to establish the cause of an effect. The technique uses a Cause and Effect Diagram to record the possible causes as they are suggested. This tool encourages a group setting for problem -solving and demonstrates that problems can have a number of causes.Ĭause and effect analysis is a technique for identifying the possible causes of a problem or effect. Also called the ‘Fishbone Diagram’, or Ishikawa chart, this participatory exercise explores the links between the effects and the possible causes of an issue.
